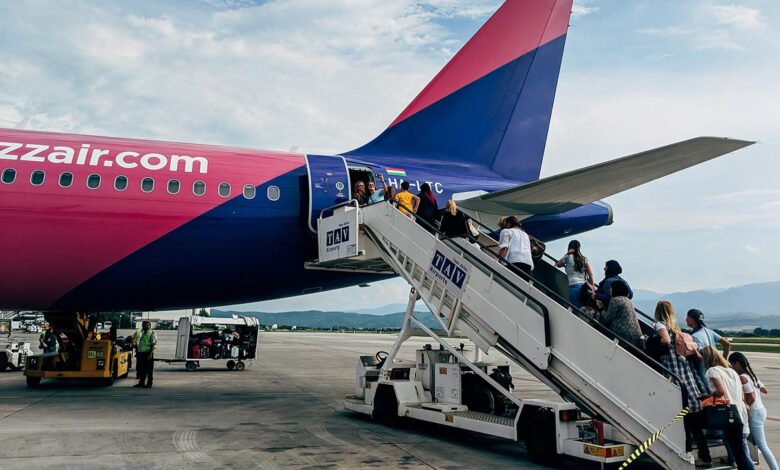
Boarding Now Flight to Quality
Boarding now the flight to quality sets the stage for a journey into the heart of quality improvement. This exploration dives deep into the metaphorical concept of “boarding a flight,” examining the urgency of “boarding now” and the ideal destination represented by “the flight to quality.” We’ll unpack the necessary methods for achieving quality improvement, along with the potential obstacles and challenges that might arise.
The journey, represented by a visual narrative, will showcase the key milestones, strategies for implementation, and the rewards for achieving excellence.
Imagine a company striving for excellence, recognizing the critical need to elevate its standards. This is where the concept of “boarding now the flight to quality” becomes crucial. It’s about embracing immediate action and commitment to the continuous improvement process. By understanding the destination, the necessary methods, and the potential obstacles, businesses can embark on a journey toward superior quality.
Defining “Boarding Now the Flight to Quality”
The phrase “boarding now the flight to quality” evokes a powerful image of transformation and progress. It suggests a deliberate and intentional movement towards a higher standard of excellence, a journey undertaken with purpose and anticipation. It’s not just about achieving quality; it’s about actively committing to a process of continuous improvement. This metaphorical flight implies a planned and structured approach to enhancing quality, not a haphazard or reactive one.The metaphor of “boarding a flight” in relation to quality improvement signifies the act of entering a structured process, a pre-planned journey with a specific destination.
This journey is not spontaneous; it’s a deliberate step taken toward a defined goal. The “flight” itself represents the period of sustained effort and focused action needed to achieve quality improvement. It suggests a period of controlled, methodical progress, with clear steps and milestones along the way.
Potential Connotations of “Quality”
The word “quality” in this context can encompass a multitude of aspects, depending on the specific context. It might refer to the quality of products, services, processes, or even the quality of relationships within an organization. It could encompass reliability, consistency, efficiency, customer satisfaction, and adherence to standards. Ultimately, the specific meaning of “quality” will depend on the context in which the phrase is used.
Examples of Situations Where the Phrase Might Be Used
This phrase could be used in a variety of settings, from business to personal development. Imagine a company implementing a new quality management system. They might use this phrase to describe the initiative. A team of software developers could use it to describe their process of refining their code for greater efficiency and reliability. A student might use it to describe their approach to improving their academic performance, emphasizing the structured effort they are putting into achieving excellence.
A personal trainer could use it to describe a client’s commitment to achieving fitness goals through a carefully designed program. The phrase is adaptable to numerous situations.
Implied Journey and Destination
The phrase “boarding now the flight to quality” implies a journey with a specific destination. The “journey” signifies the ongoing process of implementing quality improvements, the steps and challenges encountered along the way. The “destination,” representing the ultimate goal, is often the attainment of a higher standard of quality. This destination is not static; it’s a continuous process of refinement, always striving for excellence.
Boarding now the flight to quality means more than just getting on a plane. It’s about experiencing the enhanced comfort and service that comes with a refined travel experience, like the recent renovations at AK’s Sanctuary Sun IV. AK unveils renovated Sanctuary Sun IV , showcasing a commitment to excellence that truly sets a new standard. This dedication to quality carries over into every aspect of the journey, making the whole experience a delight, and we are boarding now.
The implied journey underscores the importance of a methodical approach to quality improvement. The destination represents a sustained commitment to quality, not just a one-time achievement. The journey emphasizes the ongoing nature of the pursuit, and the destination highlights the continuous aspiration for excellence.
Understanding the Context of “Boarding Now”
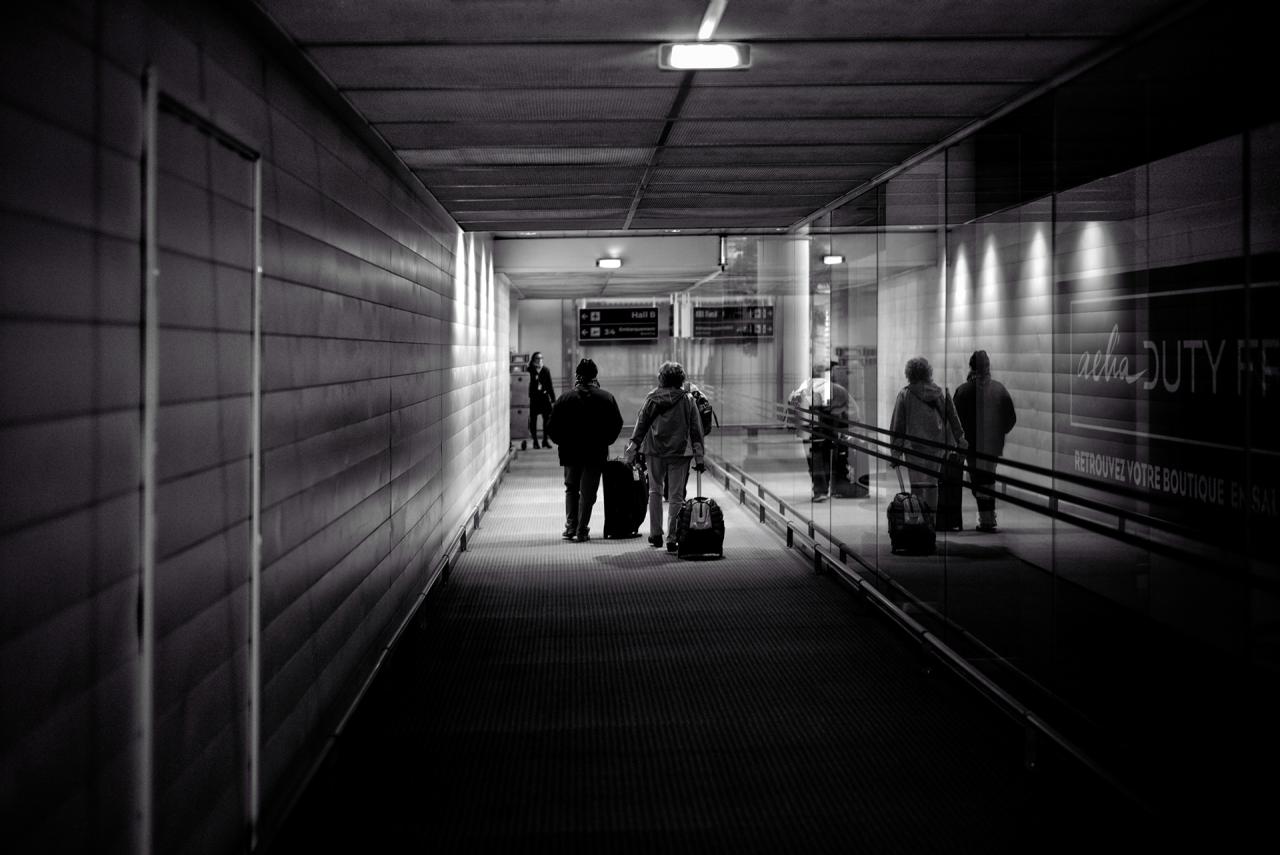
The phrase “boarding now” evokes a sense of immediate action and urgency. It’s more than just a notification; it’s a call to prioritize and mobilize resources towards a specific goal. This urgency is crucial for quality improvement, as addressing issues promptly can prevent escalation and minimize negative impact. This concept extends beyond physical travel; it represents a mindset shift in various contexts, from business operations to personal development.The phrase inherently implies a need for swift action.
It signals that the current state requires immediate attention, highlighting the importance of recognizing and responding to problems in a timely manner. The context of “boarding now” is directly tied to the concept of proactively addressing quality issues, and this proactive approach can lead to significant benefits.
Urgency and Action Implied by “Boarding Now”
“Boarding now” signifies an immediate need for action, highlighting the criticality of the situation and the need for prompt response. This emphasis on immediacy drives individuals and teams to prioritize tasks related to quality improvement. In essence, it encourages a shift in mindset from a reactive to a proactive approach. The phrase serves as a potent catalyst for change, encouraging focused efforts on rectifying issues as they arise.
Examples of Situations Requiring Immediate Action for Quality Improvement
Numerous situations demand immediate action to ensure quality improvement. A sudden spike in customer complaints about a specific product or service, a critical machine malfunction impacting production, or a significant safety breach within a facility are all instances where immediate action is paramount. Procrastination can exacerbate the problem, potentially leading to greater losses and reputational damage. For example, if a website experiences a sudden surge in traffic that causes it to crash, immediate intervention is required to identify the cause and restore functionality.
Using “Boarding Now” in a Business Setting to Motivate Employees
In a business context, using “boarding now” can be a powerful motivational tool. By framing quality improvement initiatives as an urgent boarding process, managers can foster a sense of shared responsibility and urgency among employees. This sense of collective action can drive increased engagement and productivity. For example, a company facing a decline in customer satisfaction scores might use “boarding now” to signal the need for a rapid response, galvanizing employees to identify and resolve the root causes.
Potential Challenges of Immediate Action in Quality Improvement, Boarding now the flight to quality
While immediate action is often beneficial, there are potential challenges to overcome. Rushing into solutions without proper analysis can lead to ineffective or even counterproductive measures. Insufficient data gathering, rushed decision-making, or insufficient resources can hinder the success of quick fixes. Thorough planning and meticulous execution are critical to ensure that immediate action is not at the expense of long-term solutions.
“Boarding Now” as a Call to Action
The phrase “boarding now” functions as a potent call to action, emphasizing the need for immediate involvement in a specific initiative or project. It signifies the criticality of the situation and encourages participation and dedication. The phrase fosters a sense of shared responsibility, pushing individuals and teams to work together towards a common goal, promoting a proactive and responsive attitude towards quality improvement.
Identifying the Destination
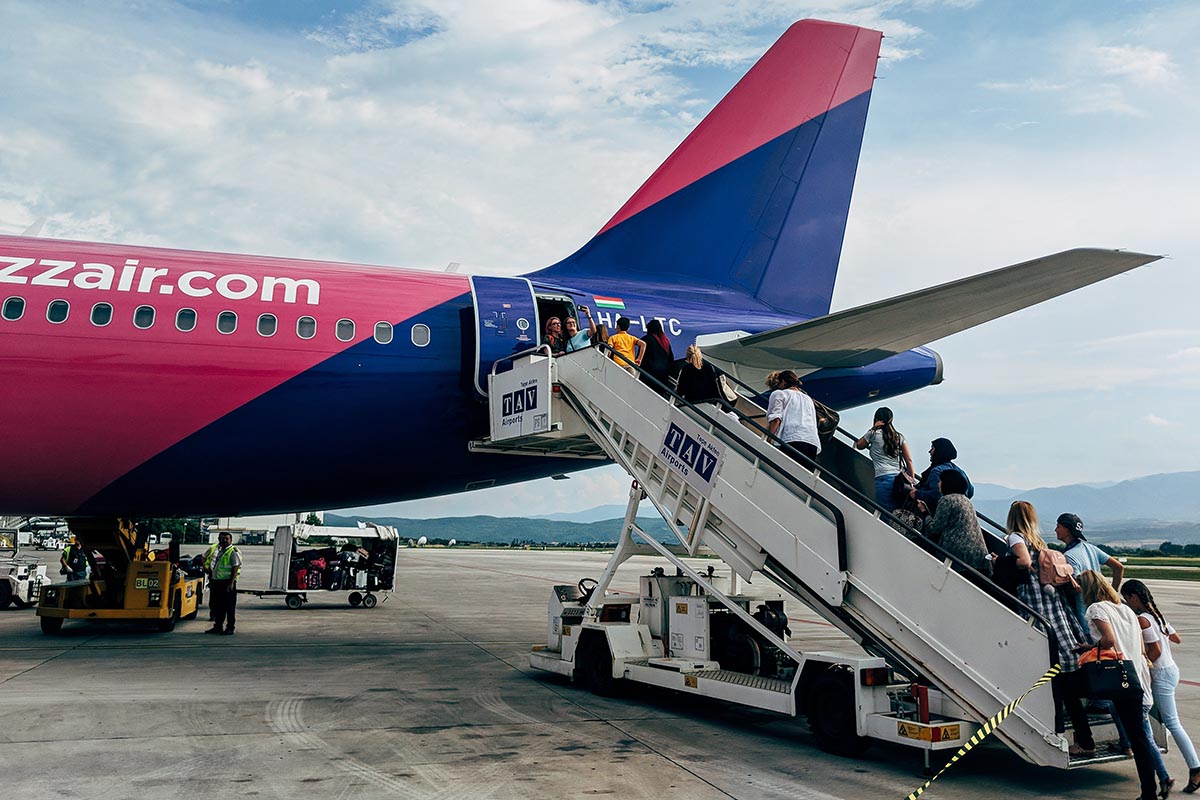
Embarking on a “flight to quality” isn’t just about reaching a destination; it’s about the continuous journey of improvement. This journey requires a clear understanding of the ideal state of quality being pursued, the characteristics of the “flight,” and the concrete examples of businesses that embody this pursuit. It’s about recognizing that quality isn’t a fixed point but a dynamic, evolving standard.The “flight to quality” represents a commitment to excellence, a dedication to exceeding expectations, and a proactive approach to continuous improvement.
This isn’t merely about meeting minimum standards; it’s about exceeding them, constantly striving for better processes, products, and customer experiences. This pursuit requires a deep understanding of the target destination.
The Ideal State of Quality
The ideal state of quality implied by “the flight to quality” is not a static definition. It encompasses a multifaceted approach, incorporating various dimensions. It’s not just about meeting specifications; it’s about exceeding customer expectations, anticipating needs, and fostering a culture of continuous improvement. It is about a holistic view of quality, including the experience of using a product or service, the environmental impact, and the ethical considerations of the process.
Characteristics of a “Flight to Quality”
A “flight to quality” is characterized by several key elements. It’s not a one-time event but an ongoing process, a journey with clearly defined stages and metrics. The journey is fueled by a commitment to learning and adapting. Key characteristics include:
- Customer Focus: A strong understanding of customer needs and preferences is paramount. This goes beyond simply meeting stated requirements; it’s about anticipating and exceeding expectations.
- Process Optimization: Continuous evaluation and improvement of internal processes are essential. Identifying bottlenecks, eliminating waste, and streamlining workflows are key components.
- Data-Driven Decision Making: Leveraging data to understand performance, identify areas for improvement, and track progress is critical. Data analysis informs decisions and ensures that efforts are focused and effective.
- Employee Empowerment: Empowering employees to contribute to the quality improvement process is vital. This fosters a sense of ownership and responsibility, encouraging creativity and innovation.
- Continuous Improvement: The journey to quality is never complete. It requires a relentless pursuit of improvement, adapting to changing market demands and customer expectations.
Examples of Businesses that Exemplify a “Flight to Quality”
Several businesses exemplify the “flight to quality.” These businesses demonstrate a commitment to excellence, a customer-centric approach, and a relentless pursuit of improvement. Examples include:
- Toyota: Renowned for its lean manufacturing processes and commitment to quality control, Toyota exemplifies continuous improvement and the importance of data-driven decision-making.
- Apple: Known for its innovative products and meticulous attention to detail, Apple demonstrates a focus on design, user experience, and meticulous quality control.
- Ikea: Ikea exemplifies a focus on efficiency and cost-effectiveness, while maintaining high-quality standards for their products and customer experience.
Levels of Quality
Quality can be categorized into different levels. The levels represent a spectrum of performance, from basic compliance to exceeding expectations.
Level | Description | Examples |
---|---|---|
Basic Compliance | Meeting minimum standards and regulations. | A product that functions as intended, but with no extra features. |
Customer Satisfaction | Meeting or exceeding customer expectations in a satisfactory manner. | A product that is functional, reliable, and provides a good user experience. |
Exceeding Expectations | Providing a superior product or service that goes beyond customer expectations. | A product with innovative features, exceptional design, and a seamless user experience. |
A Visual Representation of the Journey
The journey to quality can be visualized as a graph or a simple diagram, illustrating the stages and levels involved. This diagram can represent the continuous cycle of improvement, showing how small steps add up to significant progress.
A diagram (which I can’t create here) could represent this journey with a line graph showing a gradual increase over time. The x-axis would represent time, and the y-axis would represent a quality metric (e.g., customer satisfaction scores, defect rates). The graph would demonstrate a continuous upward trend.
Methods for Achieving Quality Improvement
Embarking on a journey toward quality improvement is not a destination, but a continuous process. It’s about constantly striving to enhance products, services, and processes. This journey requires a structured approach, understanding that improvement is not a one-time event, but a cycle of continuous learning and adaptation. The “boarding now the flight to quality” metaphor aptly captures this dynamic.
Quality Improvement Methodologies
Various methodologies exist to guide the journey toward quality. Each approach offers a unique set of tools and techniques for identifying, analyzing, and resolving quality issues. By selecting the appropriate method, organizations can more effectively address specific challenges and achieve significant improvements.
Method Name | Description | Benefits |
---|---|---|
Total Quality Management (TQM) | A comprehensive approach to quality improvement that integrates the efforts of all employees at all levels. It emphasizes customer satisfaction, continuous improvement, and employee empowerment. | Improved customer satisfaction, increased efficiency, reduced costs, and enhanced employee morale. |
Six Sigma | A data-driven methodology focused on reducing defects and variability in processes. It employs statistical tools and techniques to identify and eliminate sources of error. | Significant reduction in defects, improved process efficiency, reduced costs, and enhanced product quality. |
Lean Manufacturing | A methodology that aims to eliminate waste (muda) from manufacturing processes. It focuses on maximizing value for the customer while minimizing resources used. | Increased efficiency, reduced costs, improved lead times, and enhanced customer value. |
Kaizen | A Japanese philosophy emphasizing continuous improvement through small, incremental changes. It encourages employee participation and problem-solving at all levels. | Incremental improvements across all aspects of operations, reduced waste, and enhanced employee engagement. |
Implementing Quality Improvement Methods
Implementing any quality improvement method requires a systematic approach. The steps involved vary depending on the specific method, but typically include:
- Define the problem: Clearly identify the specific area needing improvement and define the desired outcome.
- Measure the current state: Collect data to understand the current performance level and identify areas of weakness.
- Analyze the causes of the problem: Investigate the root causes of the quality issues, using tools like fishbone diagrams or Pareto charts.
- Develop solutions: Create and implement solutions to address the root causes of the problems.
- Implement the solutions: Carefully deploy the chosen solutions and monitor their effectiveness.
- Control the process: Establish procedures to maintain the improvements and prevent the quality issues from recurring.
Examples of Successful Implementations
- Toyota, renowned for its lean manufacturing practices, has significantly reduced waste and improved efficiency across its production lines, resulting in higher quality vehicles and reduced costs. This exemplifies the effectiveness of a well-structured methodology in achieving operational excellence.
- Motorola‘s pioneering work with Six Sigma methodologies led to a substantial reduction in product defects and improved customer satisfaction. Their commitment to data-driven problem-solving and process improvement showcased the power of rigorous statistical analysis in achieving quality goals.
Obstacles and Challenges to Quality Improvement
Embarking on a journey to enhance quality often faces unforeseen hurdles. Understanding these obstacles and developing strategies to overcome them is crucial for a successful transformation. This section delves into potential challenges, mitigation strategies, and real-world examples of businesses that have navigated similar difficulties.
Resistance to Change
Resistance to change is a pervasive obstacle in quality improvement initiatives. Employees may fear job security, feel uncomfortable with new processes, or simply resist adopting unfamiliar methods. This resistance can manifest in various ways, including passive resistance, open opposition, or subtle sabotage.
Boarding now the flight to quality, I’m excited to see what’s brewing on the Big Island! The local coffee scene is buzzing with activity, and I’m particularly keen to check out the exciting coffee fest that’s happening there. Big Island brews up big things for coffee fest , promising a rich experience for all coffee aficionados. Hopefully, this will be a huge boost to my journey to quality, as I learn more about the process.
Looking forward to taking in all the quality offerings!
Lack of Resources
Implementing quality improvement initiatives often requires significant resources, including financial capital, time, and skilled personnel. Insufficient budget allocation, lack of dedicated time for training, or a shortage of experienced personnel can severely impede progress.
Lack of Commitment from Leadership
Quality improvement initiatives require strong leadership support. Without active commitment from upper management, initiatives may lack the necessary drive and momentum to succeed. A lack of clear communication, inadequate prioritization, or insufficient resources allocated can reflect a lack of leadership commitment.
Inadequate Training and Support
Employees need proper training and support to effectively implement new quality improvement procedures. Insufficient training can lead to errors, inefficiencies, and ultimately, a failure to achieve desired outcomes. Without sufficient support and guidance, employees may struggle to adapt to the new processes and systems.
Boarding now the flight to quality, I’m excited to see what adventures await. After my recent China sojourn, I’m especially interested in the updated Norwegian Joy for Alaska cruises, as detailed in this fascinating article about the ship’s recent modifications after china sojourn norwegian joy updated for alaska. Hopefully, this new experience will help me refine my travel approach and make my future trips even more enjoyable.
So, boarding now the flight to quality, let’s see where it takes us!
Data Collection and Analysis Challenges
Accurate data collection and analysis are essential for identifying areas for improvement. Difficulties in collecting accurate data, challenges in data interpretation, or a lack of expertise in statistical analysis can hinder the ability to pinpoint problem areas and measure progress. This can result in ineffective strategies and a failure to track improvement.
External Factors
External factors, such as fluctuating market conditions, supply chain disruptions, or regulatory changes, can impact quality improvement efforts. These unforeseen external factors can derail planned projects and require adjustments to strategies. A proactive approach to assessing and mitigating external risks is essential.
Overcoming Obstacles
To overcome these obstacles, a multifaceted approach is required. This includes fostering a culture of continuous improvement, providing adequate resources, and securing leadership support. Clear communication, transparency, and consistent reinforcement are vital for effective implementation.
Risk Mitigation Strategies
Effective risk mitigation strategies are crucial for quality improvement projects. These strategies include proactive planning, thorough risk assessment, contingency planning, and regular monitoring. A well-defined risk register that documents potential risks, their likelihood, and impact, is a critical tool for managing quality improvement projects.
Real-World Examples
Numerous businesses have successfully navigated quality challenges. For instance, Toyota’s commitment to continuous improvement, through its lean manufacturing principles, has resulted in significant quality enhancements. Similarly, companies like Motorola have implemented robust quality management systems that have driven significant improvements in product quality.
Planning and Risk Assessment
Planning and risk assessment are paramount for successful quality improvement. A well-defined plan that identifies potential obstacles, their likelihood, and potential impact is essential. Proactive risk management, including contingency plans and regular monitoring, can significantly reduce the negative impact of unexpected challenges.
Illustrating the Journey to Quality: Boarding Now The Flight To Quality
Embarking on a journey towards quality improvement is akin to boarding a plane. It’s a process filled with anticipation, challenges, and ultimately, the rewarding destination of excellence. This section will explore the visual representation of this journey, from takeoff to landing, highlighting the obstacles, milestones, and stages involved.
Visualizing the Flight to Quality
The journey to quality improvement can be effectively visualized as a plane taking off. The plane’s powerful engines represent the initial impetus for change, fueled by a strong commitment to improvement. The runway, stretching into the distance, symbolizes the long-term vision and the extensive work required.
Obstacles Encountered
The journey to quality improvement is rarely smooth. Obstacles are inevitable, like turbulence encountered during flight. Visualizing these obstacles is crucial to understanding and mitigating their impact. Imagine a series of clouds and storms, representing various challenges, such as resistance to change, lack of resources, or unexpected setbacks. These obstacles can be visualized as a series of dark clouds or turbulent weather patterns that the plane must navigate.
Each cloud could represent a specific challenge – a lack of employee buy-in, outdated technology, or inadequate training. These challenges can be surmounted with careful planning, proactive problem-solving, and a resilient attitude.
Key Milestones in the Quality Improvement Flight
Visualizing the milestones of the quality improvement journey can be represented as a detailed infographic. This infographic would show the various stages of the journey as distinct checkpoints along the flight path. The milestones would include key achievements, like successful implementation of new processes, improved customer satisfaction scores, or reduced defect rates. The infographic would help teams track progress and celebrate successes along the way.
For example, a milestone might be represented by a marker on the infographic at a specific altitude or geographical location.
Boarding now the flight to quality feels exciting, especially considering the recent shift in travel trends. An interesting arc study reveals a growing trend toward one-way ticket sales, arc study reveals a growing trend toward one way ticket sales , suggesting a more flexible and potentially budget-friendly approach to travel. This could be a game changer for those seeking unique and extended adventures, further fueling the journey to quality.
Stages of the Quality Improvement Journey
The journey to quality improvement is not a single event but a continuous process. It comprises several distinct stages, analogous to different phases of a flight. The initial phase, often likened to the pre-flight checklist, involves setting clear goals and objectives. The next stage, corresponding to taxiing, includes thorough planning and preparation. The take-off phase involves initiating the improvement project.
The flight phase includes ongoing monitoring, adjustments, and course corrections. The landing phase represents the successful implementation and stabilization of the new quality standards.
Rewards and Recognition
Achieving quality standards is not just about the journey but also the destination. Rewards and recognition are essential to motivate teams and reinforce the importance of quality improvement. These rewards can range from monetary incentives, to public recognition, to internal promotions. The rewards are like the accolades and celebrations upon successful landing, signaling the successful completion of the journey and highlighting the commitment and dedication of the team.
Implementing Strategies for Quality Improvement
Embarking on a journey toward quality improvement necessitates a structured approach, transforming aspirations into tangible results. This involves translating abstract concepts into practical steps, enabling organizations to consistently deliver high-quality products or services. The “boarding now” concept, signifying immediate action and proactive engagement, is crucial in this process.Effective quality improvement isn’t a one-time event but an ongoing process.
Boarding now the flight to quality means focusing on improvements, and the recent developments in the ARC NDC working group could yield real results here. This collaborative effort promises better travel experiences and streamlined processes, ultimately pushing us towards a higher standard of quality in the travel industry. It’s exciting to see this progress, and I’m optimistic about the future of travel.
It demands a commitment to continuous learning, adaptation, and improvement. This commitment requires a well-defined strategy, clear roles and responsibilities, and a supportive environment. Implementing this strategy necessitates a methodical approach, ensuring each step is carefully considered and executed.
Actionable Strategies for Workplace Implementation
Implementing quality improvement strategies in a workplace requires a multifaceted approach. It’s essential to understand that improvement is not a singular solution but a collective effort that involves every member of the organization. This section Artikels actionable strategies to transform the “boarding now” concept into practical actions.
- Establish Clear Quality Metrics: Defining quantifiable metrics for quality ensures that improvements can be measured and tracked. Examples include customer satisfaction scores, defect rates, and production cycle times. This establishes a benchmark for assessing progress and identifying areas needing further attention. These metrics must be relevant to the specific organization’s goals and industry standards.
- Foster a Culture of Continuous Improvement: Creating a culture where employees feel empowered to identify and suggest improvements is paramount. This necessitates open communication channels, recognition for contributions, and a safe environment for sharing ideas. Regular feedback mechanisms and suggestion boxes play a vital role in this process.
- Implement Training and Development Programs: Equipping employees with the skills and knowledge needed to deliver high-quality work is crucial. Training programs should focus on relevant quality improvement methodologies and tools, such as Lean Six Sigma or Total Quality Management.
- Encourage Teamwork and Collaboration: Quality improvement is a team effort. Promoting teamwork and collaboration among employees in different departments helps break down silos and fosters a shared understanding of quality goals.
Practical Steps for Immediate Action
These practical steps, designed for immediate action, can be utilized across various organizations.
- Identify Key Quality Issues: Conduct a thorough assessment of current processes and identify areas where quality is lacking. Data analysis and employee feedback are vital for accurate identification.
- Develop Action Plans: For each identified issue, develop a specific action plan outlining the steps required for improvement. This should include timelines, responsible parties, and expected outcomes.
- Implement Solutions: Put the action plans into effect, ensuring that the allocated resources and personnel are available. Monitor progress diligently.
- Evaluate and Adjust: Regularly evaluate the effectiveness of implemented solutions. Adapt plans as needed to optimize results.
Workflow Diagram for Implementation Process
[A simplified workflow diagram illustrating the process of identifying quality issues, developing action plans, implementing solutions, and evaluating results would be placed here. The diagram would visually represent the sequential nature of these steps, showcasing the interconnectedness of each phase.]
Implementation Steps Table
Step | Description | Responsible Party |
---|---|---|
1 | Identify key quality issues | Quality Improvement Team |
2 | Develop action plans for each issue | Project Leaders/Team Leads |
3 | Implement solutions and monitor progress | All relevant departments |
4 | Evaluate and adjust plans as needed | Quality Improvement Team |
Adapting Strategies to Different Organizational Structures
The strategies Artikeld above can be adapted to various organizational structures. For instance, in a matrix organization, collaboration and communication between different teams are crucial. In a hierarchical structure, clear communication channels and delegation of responsibilities are essential. Flexibility and adaptability are key to successful implementation across diverse organizational settings.
Ending Remarks
In conclusion, “boarding now the flight to quality” isn’t just a catchy phrase; it’s a call to action, a commitment to excellence, and a journey of continuous improvement. This exploration highlights the importance of immediate action, strategic planning, and meticulous execution in achieving superior quality. By implementing the methods discussed, overcoming the challenges Artikeld, and maintaining a focus on the desired destination, businesses can embark on a rewarding flight toward quality excellence.
Clarifying Questions
What are some common obstacles to quality improvement?
Resistance to change, lack of resources, inadequate training, and poor communication are among the frequent obstacles that hinder quality improvement initiatives.
How can businesses effectively overcome these obstacles?
Addressing resistance through clear communication and employee involvement, allocating necessary resources, providing comprehensive training, and fostering open communication channels are crucial steps in overcoming these obstacles.
What are some practical examples of quality improvement strategies?
Implementing Six Sigma methodologies, Lean principles, and Total Quality Management (TQM) frameworks can significantly contribute to quality improvement efforts. Continuous monitoring and evaluation are essential for sustained progress.
What role does leadership play in driving quality improvement initiatives?
Strong leadership is essential for creating a culture of quality and fostering employee engagement. Leaders should champion the initiative, provide resources, and actively participate in the process.