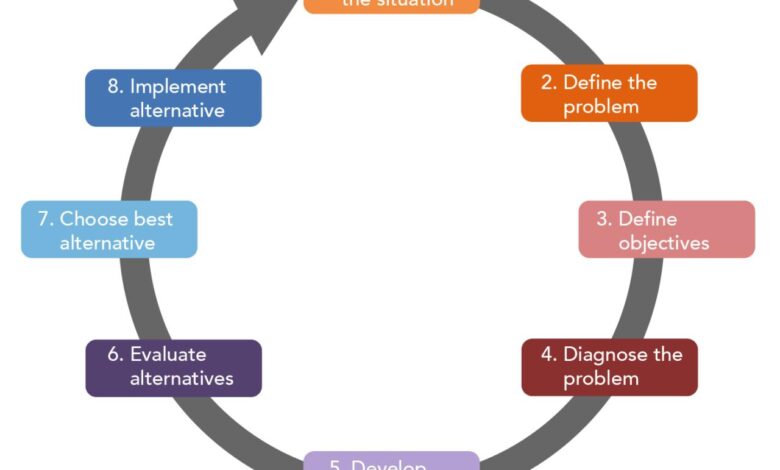
Rational Ship Orders A Practical Guide
Arison on ship orders it has to be done rationally sets the stage for a discussion on optimizing shipping operations. This isn’t just about following procedures; it’s about understanding the intricate factors that influence ship order prioritization and implementing a system that leads to greater efficiency and profitability.
This comprehensive guide explores the principles of rational decision-making in ship orders, from detailed explanations of the process to practical case studies. We’ll delve into the steps, criteria, and factors involved in prioritizing ship orders effectively, examining various methods for optimizing processes and mitigating potential risks. The ultimate goal is to provide a clear and actionable roadmap for implementing a rational approach to ship order management.
Rational Decision-Making in Shipping Orders
Optimizing shipping orders requires a structured, data-driven approach. Simply reacting to immediate needs often leads to inefficiencies and missed opportunities for cost savings and improved delivery times. A rational framework allows for proactive planning and execution, resulting in better overall outcomes. This framework considers various factors, enabling companies to make informed decisions that maximize profitability and minimize risks.Rational decision-making, in the context of shipping orders, involves a systematic process that considers all relevant information and potential outcomes.
This involves defining clear objectives, gathering comprehensive data, evaluating alternatives, and selecting the option that best aligns with the established goals. This approach contrasts with intuitive or emotional decision-making, which may be influenced by biases or incomplete information.
Principles of Rational Decision-Making
Rational decision-making in shipping relies on several key principles. These include identifying the problem, gathering data, defining objectives, and evaluating potential solutions. Each option should be assessed against predefined criteria. The final decision should be the one that most effectively achieves the established objectives while minimizing negative impacts. Transparency in the process and communication across relevant departments are crucial for effective implementation.
Steps in Rational Ship Order Prioritization
A rational approach to ship order prioritization involves several sequential steps. Firstly, defining clear criteria for evaluating orders is essential. These criteria might include urgency, cargo type, destination, and vessel availability. Next, gather data on each order, including the specifics mentioned above. Analyze this data, considering potential impacts on other orders and the overall operational efficiency.
After evaluating the various options, select the most suitable order based on the predetermined criteria. Finally, monitor and evaluate the effectiveness of the chosen strategy to identify areas for improvement. This iterative process allows for continuous refinement of the prioritization method.
Criteria for Evaluating Ship Order Efficiency
Evaluating ship order efficiency involves multiple criteria. These criteria are critical to measuring the success of a chosen prioritization strategy. Examples include on-time delivery rates, cargo damage rates, and total transportation costs. Other critical criteria include minimizing vessel idle time and ensuring optimal cargo space utilization. A detailed analysis of these factors provides valuable insights for continuous improvement.
Factors Impacting Ship Order Prioritization
Several factors significantly influence the prioritization of ship orders. These factors are critical to consider in any rational decision-making process. Understanding these factors allows for a more comprehensive and nuanced approach to ship order management.
Factor | Description | Impact on Decision | Mitigation Strategy |
---|---|---|---|
Cargo Type | Different cargo types have varying handling requirements and safety regulations. | High-value or perishable goods require prioritized handling and delivery. Fragile cargo might require special handling procedures. | Establish clear procedures for handling specific cargo types. Develop a system to track and monitor the handling of each order. |
Destination | Distance and geographic location of the destination influence transportation time and costs. | Orders destined for remote locations may require longer transit times, increasing the potential for delays. | Utilize predictive analytics to account for potential delays and factor them into prioritization. |
Vessel Availability | The availability of suitable vessels with appropriate capacity and schedule significantly impacts the feasibility of shipping orders. | Lack of available vessels may delay order processing, affecting on-time delivery. | Maintain a comprehensive vessel schedule and availability database. Develop contingency plans for unexpected vessel delays or unavailability. |
Order Urgency | The urgency of the delivery significantly influences the prioritization of the order. | Orders with urgent delivery requirements should be prioritized to avoid potential losses or revenue impacts. | Implement a clear system for classifying orders by urgency level. Track deadlines and potential delays in each order’s processing. |
Cargo Volume and Weight | The volume and weight of cargo can influence the choice of vessel and transport methods. | Large volumes or heavy cargo might require specialized vessels or handling procedures. | Develop a system to predict cargo volume and weight demands. Ensure vessel selection aligns with cargo size and weight specifications. |
Optimizing Ship Order Processes
Ship orders, a critical component of the maritime industry, require meticulous planning and execution. Efficient management of these orders directly impacts profitability, delivery times, and overall operational efficiency. Rational decision-making, as previously discussed, is paramount to achieving these objectives. This section delves into optimizing ship order processes, examining frameworks, methodologies, and potential bottlenecks.Effective ship order management transcends simple paperwork; it encompasses a sophisticated interplay of human expertise, technology, and data analysis.
This requires a structured approach that encompasses all stages of the process, from initial inquiry to final delivery. This structured approach allows for better forecasting and resource allocation.
Rational Ship Order Management Framework
A rational ship order management system should be designed with a clear, hierarchical structure. The framework must encompass a comprehensive set of guidelines and procedures that are standardized, transparent, and easily adaptable to changing market conditions. This framework will encompass every stage of the ship order, from initial inquiry to final delivery. Crucially, the framework must align with the overarching organizational goals and strategies.
Comparison of Ship Order Handling Methods
Different methods for handling ship orders exist, each with unique strengths and weaknesses.
- Manual Systems: Manual systems often rely on paper-based documentation and manual data entry. While potentially less expensive initially, these systems are prone to errors, lack real-time visibility, and struggle to handle the complexities of large-scale operations. Their limited tracking capabilities and potential for data loss significantly hinder the rational decision-making process.
- Automated Systems: Automated systems utilize software applications and digital platforms to manage ship orders. This allows for real-time tracking, streamlined communication, and data-driven decision-making. Automation enhances accuracy and efficiency. However, the initial investment in software and training can be substantial, and the dependence on technology may present challenges in cases of system failure.
Potential Bottlenecks in Ship Order Processing
Identifying bottlenecks is crucial for streamlining ship order processing. Common bottlenecks include inefficient communication channels, delays in obtaining necessary approvals, and overloaded staff handling multiple tasks simultaneously. A bottleneck in one area of the process can have a ripple effect, impacting the entire workflow. This often manifests as extended lead times, lost revenue, and customer dissatisfaction.
Data Analytics in Optimizing Ship Order Processes
Data analytics plays a critical role in optimizing ship order processes. Analyzing historical data on ship orders, market trends, and operational performance allows for proactive identification of potential issues and informed decision-making. This allows for improved resource allocation, leading to more accurate cost estimations, better project planning, and reduced risks. For example, analyzing past delivery times allows for more realistic delivery estimations for new orders.
Deciding on ship orders for Arison requires a rational approach. It’s all about strategic planning, and sometimes, the best decisions come from considering the bigger picture. Just like savoring the delightful flavors at Weston’s new Avenue117 candy taste buds dance at westons new avenue117 candy , a careful balance of factors must be considered. Ultimately, a rational strategy ensures the best possible outcome for Arison’s operations.
Measuring Effectiveness of the Rational Approach
Measuring the effectiveness of a rational approach to ship orders requires quantifiable metrics. Key performance indicators (KPIs) should focus on order fulfillment time, cost efficiency, error rates, and customer satisfaction. Tracking these KPIs allows for continuous improvement and ensures that the chosen methods are effectively addressing the specific needs of the business. For instance, a reduction in order fulfillment time or a decrease in errors are clear indicators of a successful implementation of a rational approach.
Monitoring these metrics regularly provides valuable feedback and data for making informed decisions and refinements to the ship order process.
Risk Assessment and Mitigation in Ship Orders
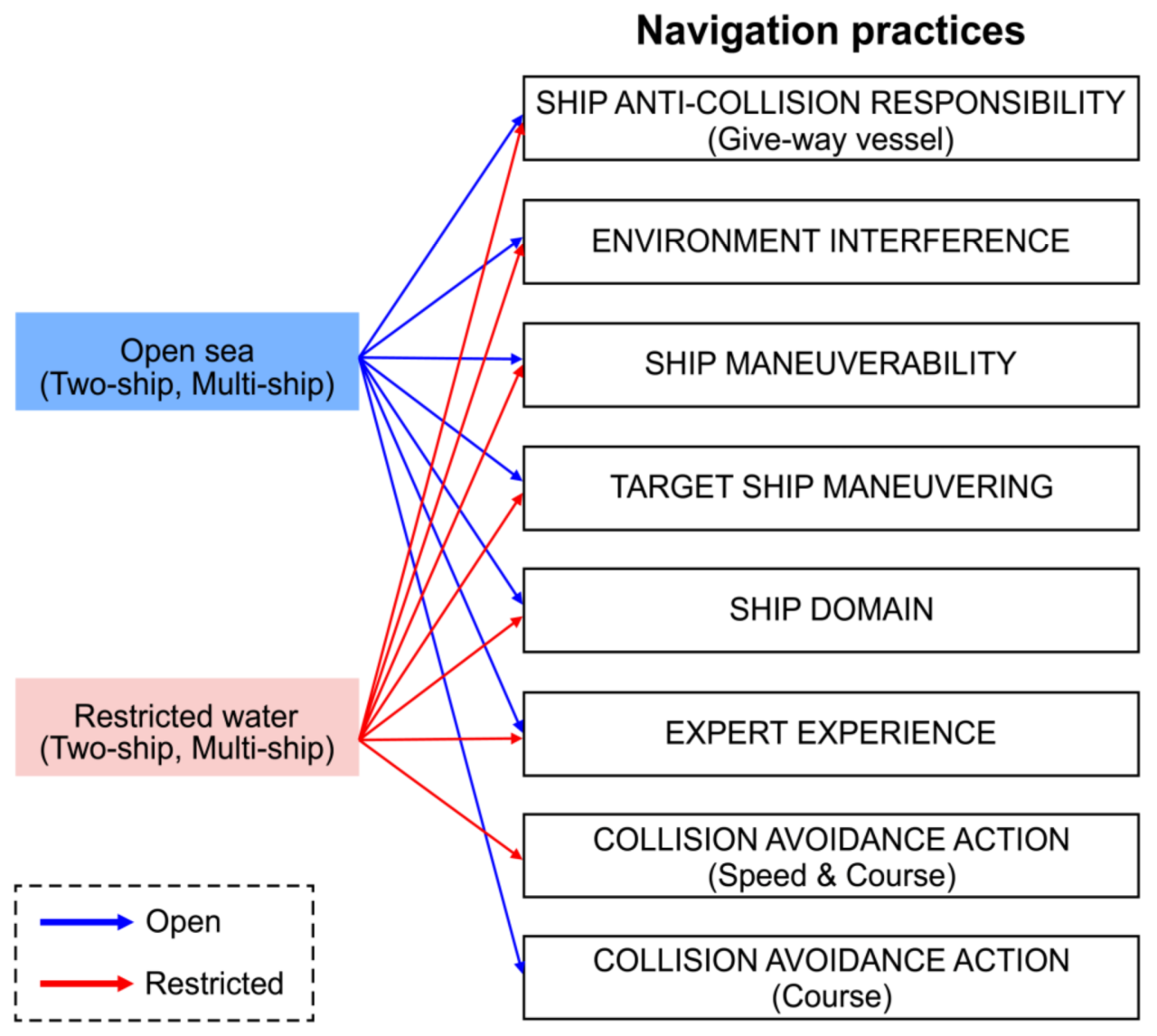
Rational ship order management isn’t just about cost and schedule; it’s also about anticipating and mitigating potential problems. A robust risk assessment process is crucial for making informed decisions and navigating the complexities of the shipping industry. Ignoring potential pitfalls can lead to costly delays, financial losses, and reputational damage.A proactive approach to risk assessment allows ship owners and managers to anticipate challenges and develop contingency plans.
This approach ensures that ship orders are not only financially viable but also practically achievable and legally sound. Understanding the potential risks associated with each stage of the ship order process allows for a more realistic and effective management strategy.
Structured Approach to Risk Assessment
A structured approach to risk assessment is essential for identifying and prioritizing potential issues. This approach involves a systematic process of identifying potential threats, evaluating their likelihood and impact, and developing mitigation strategies. A detailed checklist should include factors like design specifications, construction timelines, and regulatory compliance.
Risk Categories
Risk assessment involves categorizing potential issues into manageable groups for clarity and focused mitigation. Categorization into operational, financial, and legal risks allows for targeted interventions and prevents overlap.
- Operational Risks: These risks pertain to the day-to-day activities of the ship and its operation. Examples include equipment malfunctions, crew shortages, adverse weather conditions, and navigational errors. These factors can impact the schedule and efficiency of the shipping operation.
- Financial Risks: These risks concern the financial aspects of the ship order. Examples include fluctuations in material costs, delays in payments, and changes in market demand. Unforeseen financial shifts can impact the profitability of the project.
- Legal Risks: These risks relate to the legal framework surrounding ship orders. Examples include changes in maritime regulations, disputes with contractors, and potential liabilities. Compliance with the law is critical to avoid legal issues.
Examples of Potential Risks
Understanding the specific risks associated with each category is crucial for effective mitigation. Here are some examples within each risk category:
Risk Category | Potential Risk Example |
---|---|
Operational | A sudden and prolonged period of adverse weather conditions causing delays in construction or hindering the vessel’s initial voyage. |
Financial | A significant increase in the price of steel, a key construction material, impacting the overall project budget. |
Legal | Changes in international maritime regulations requiring costly retrofits to the vessel to comply with new standards, potentially increasing the ship’s construction cost and delaying the delivery date. |
Methods for Mitigating Identified Risks
Identifying risks is only the first step. Developing and implementing effective mitigation strategies is crucial. These strategies should be tailored to the specific risk and its potential impact.
Rational decision-making is crucial when considering ship orders, especially for a company like Arison. Recent news of American cruise lines launching an agent portal, like this one , highlights the importance of strategic partnerships and efficient processes. Ultimately, Arison needs to carefully weigh all factors, including market trends and potential partnerships, to ensure their ship orders are sound investments, not just impulsive decisions.
- Contingency Planning: Creating detailed contingency plans for various potential operational disruptions is crucial. This could involve alternative routes, backup crew members, or spare parts inventory.
- Hedging Strategies: For financial risks, implementing hedging strategies can help to mitigate the impact of price fluctuations on material costs. These strategies could include forward contracts or options.
- Legal Due Diligence: Conducting thorough legal due diligence can help to identify and mitigate potential legal risks. This involves reviewing contracts, regulations, and other relevant legal documents.
Integrating Risk Assessment into the Decision-Making Process
Integrating risk assessment into the decision-making process ensures that risk considerations are incorporated at every stage of the ship order process.
“Risk assessment should be a continuous process, not a one-time event.”
This involves regular reviews of the risk register, updates to mitigation strategies, and adjustments to the overall plan based on new information or changing circumstances.
Arison’s ship order decisions need careful consideration, and it’s crucial to approach them logically. The recent Allure of the Seas refurbishment, for example, highlights the importance of thoughtful planning when making major investments. A smart approach to ship orders, like the one Arison likely took, considers not only initial costs but also the long-term financial impact and potential return on investment, as seen in the example of the allure of the seas refurbishment.
Ultimately, rational decision-making is key for any successful shipping company.
Implementing a Rational Approach
A rational approach to ship order prioritization is crucial for optimizing vessel utilization and maximizing profitability. This involves moving beyond subjective judgments and relying on data-driven analysis to determine the most advantageous order of ship deployments. This structured process not only improves efficiency but also enhances risk mitigation by considering various factors like market demand, operational constraints, and potential disruptions.Implementing a rational approach requires a shift in mindset, embracing data analysis and algorithmic decision-making.
This transformation will increase efficiency, allowing for better resource allocation and improved profit margins. By implementing this rational approach, shipping companies can navigate the complexities of the market with greater precision and agility.
Prioritization Methodology
A well-defined prioritization methodology is essential for a rational approach. It should encompass several key factors, including expected revenue, potential delays, and associated risks. For example, a ship order with a higher estimated revenue and a shorter expected delivery time should receive a higher priority than an order with lower revenue and a longer lead time. A standardized scoring system based on weighted criteria can help quantify these factors and provide a clear ranking of ship orders.
This structured methodology provides a clear and consistent way to make decisions based on quantifiable data rather than subjective preferences.
Necessary Resources
Implementing a rational approach requires specific resources to function effectively. These include personnel with analytical and technical skills to manage and interpret data, software to support the data analysis process, and access to relevant and reliable data sources. Personnel trained in data analysis, forecasting, and risk assessment are crucial. Robust software tools for data aggregation, processing, and visualization are also essential.
Furthermore, access to real-time market data, historical performance data, and operational constraints data is necessary. The availability of these resources will directly impact the success of the rational approach implementation.
Phased Implementation Plan
A phased implementation plan is vital for a smooth transition to a rational decision-making system. This plan should be structured in a way that minimizes disruption and maximizes the utilization of existing resources.
- Phase 1: Data Collection and Preparation: This initial phase focuses on gathering relevant data, cleaning and preparing it for analysis. Key tasks include identifying data sources, standardizing data formats, and establishing data security protocols. The goal is to ensure accurate and consistent data for all subsequent phases.
- Phase 2: System Development and Testing: In this phase, software tools and algorithms are developed and tested for accuracy and efficiency. This involves establishing a system architecture, designing the algorithms, and validating the model against historical data. This phase is critical for ensuring the system’s functionality and reliability before full implementation.
- Phase 3: Training and Communication: This phase involves training personnel on the new system and communicating the rational approach to stakeholders. This includes workshops, online resources, and regular updates to ensure all parties understand the process and are prepared to utilize it. This phase focuses on stakeholder engagement and ensuring smooth transition.
- Phase 4: Full Implementation and Monitoring: In this final phase, the rational approach is implemented across all ship order processes. Monitoring the system’s performance is essential to identify any areas needing adjustment. This includes analyzing the results, tracking key metrics, and making necessary refinements to optimize the system.
Step-by-Step Procedure
The transition to the new system should be implemented incrementally, ensuring a smooth and efficient process.
- Assessment: Evaluate current ship order processes and identify areas for improvement. Determine the key metrics to track for success.
- Data Collection: Gather relevant data, standardize formats, and ensure data quality.
- System Design: Develop a rational approach to ship order prioritization. Establish algorithms and scoring systems.
- Pilot Testing: Test the system on a limited subset of ship orders. Collect feedback and make necessary adjustments.
- Full Implementation: Gradually implement the new system across all ship orders. Monitor performance and identify any issues.
- Continuous Improvement: Regularly review and refine the system based on performance data and feedback.
Stakeholder Communication
Clear communication is crucial for successful implementation. This involves transparently explaining the rationale behind the new system, addressing concerns, and ensuring buy-in from all stakeholders. Regular updates, presentations, and Q&A sessions can effectively communicate the new system and approach.
Implementation Timeline and Resources
Phase | Task | Timeline | Resources | Responsible Party |
---|---|---|---|---|
Phase 1 | Data Collection | 1 month | Data analysts, IT support | Data Management Team |
Phase 1 | Data Preparation | 2 months | Data analysts, software licenses | Data Management Team |
Phase 2 | System Development | 3 months | Software developers, IT support | IT Department |
Phase 2 | System Testing | 1 month | Testers, data analysts | IT Department |
Phase 3 | Training | 2 weeks | Training materials, trainers | Training Department |
Phase 3 | Communication | 2 weeks | Presentations, communication materials | Communication Team |
Phase 4 | Full Implementation | 1 month | All personnel, software licenses | Shipping Operations |
Phase 4 | Monitoring and Evaluation | Ongoing | Monitoring tools, data analysts | Shipping Operations, Management |
Case Studies of Successful Rational Ship Order Management
Rational ship order management isn’t just a theoretical concept; it’s a practical approach that numerous companies have successfully implemented. These case studies showcase how strategic planning, meticulous risk assessment, and efficient processes translate into tangible results. Examining these successful implementations provides valuable insights for optimizing your own ship order procedures and achieving greater profitability and operational efficiency.
This exploration delves into real-world examples, highlighting the key strategies employed by companies that have successfully navigated the complexities of ship ordering. From identifying market trends to mitigating potential risks, these case studies demonstrate the importance of a data-driven, rational approach to ship procurement.
Successful Implementations of Rational Ship Order Management, Arison on ship orders it has to be done rationally
Several companies have achieved significant improvements in their ship order management processes by adopting a rational approach. This includes meticulously defining their requirements, conducting thorough market research, and implementing robust risk assessment protocols. These approaches often result in substantial cost savings and improved project timelines.
Rational decision-making is key when it comes to Arison ship orders. You have to consider every factor, from guest preferences to the budget. Just imagine the sheer logistical dance required! A peek into the life of a top chef, like the one featured in a day in the life hal executive chef , highlights the meticulous planning needed to create a culinary experience.
The same level of thoughtful consideration applies to the planning of the entire cruise, ensuring every aspect aligns with the overall vision, ultimately leading back to that need for rational ordering of supplies.
- Maersk’s Container Ship Ordering: Maersk, a global shipping giant, implemented a sophisticated model that incorporated market analysis, projected demand, and long-term fleet planning. Their process incorporated predictive modeling to forecast future demand, enabling them to optimize their ordering strategies based on accurate estimations. This approach led to a significant reduction in ordering costs and a streamlined procurement process, impacting their overall profitability positively.
- Hyundai Heavy Industries’ Design Optimization: Hyundai Heavy Industries (HHI), a leading shipbuilder, employed advanced design optimization software to analyze various ship designs and their associated costs. By employing computational fluid dynamics (CFD) and other simulation techniques, HHI was able to improve the fuel efficiency of their designs, leading to significant cost reductions for their clients over the lifetime of the vessel. This exemplifies how rational ship ordering integrates design and construction stages for greater efficiency.
- MSC’s Fleet Expansion Strategy: Mediterranean Shipping Company (MSC), another major shipping line, established a clear fleet expansion strategy based on detailed market research. They analyzed global trade routes, anticipated demand growth, and considered the economic implications of different ship sizes and types. Their rational approach to ship ordering enabled them to procure the right vessels at the optimal time, reducing capital expenditure and optimizing their return on investment.
Common Themes in Successful Implementations
Several common threads weave through the successful ship order management cases. These include the importance of accurate market analysis, meticulous risk assessment, and efficient communication throughout the entire procurement process.
- Comprehensive Market Analysis: A thorough understanding of the market, including demand forecasts, price fluctuations, and competitor activities, is critical. Companies often use market research data, historical trends, and industry projections to inform their ship order decisions.
- Proactive Risk Assessment: Thorough risk assessment is essential, covering potential fluctuations in fuel prices, regulatory changes, and changes in demand. A rational approach accounts for these potential risks, mitigating their impact on the overall project.
- Streamlined Communication Channels: Clear and concise communication between stakeholders, including ship owners, shipbuilders, and financial institutions, is crucial. Well-defined communication channels streamline the ordering process, minimizing delays and misunderstandings.
Metrics for Measuring Success
Evaluating the effectiveness of a rational ship order management strategy requires clear metrics. These metrics should directly reflect the impact of the strategy on key business performance indicators (KPIs).
Metric | Description | Impact |
---|---|---|
Ordering Cost | Total cost associated with procuring a ship | Lower ordering costs translate to increased profitability. |
Project Timeline | Time taken to complete the entire ship order process | Shorter timelines reduce operational costs and enhance efficiency. |
Return on Investment (ROI) | Profit generated relative to the initial investment | A higher ROI indicates a successful investment decision. |
Fuel Efficiency | Measure of fuel consumption per unit of transport | Higher fuel efficiency leads to reduced operating costs. |
Impact on Profitability and Efficiency
Rational ship order management strategies demonstrably enhance profitability and efficiency by minimizing risks, optimizing costs, and streamlining the entire process. These factors contribute directly to a more stable and profitable business model in the shipping industry.
Potential Challenges and Solutions: Arison On Ship Orders It Has To Be Done Rationally
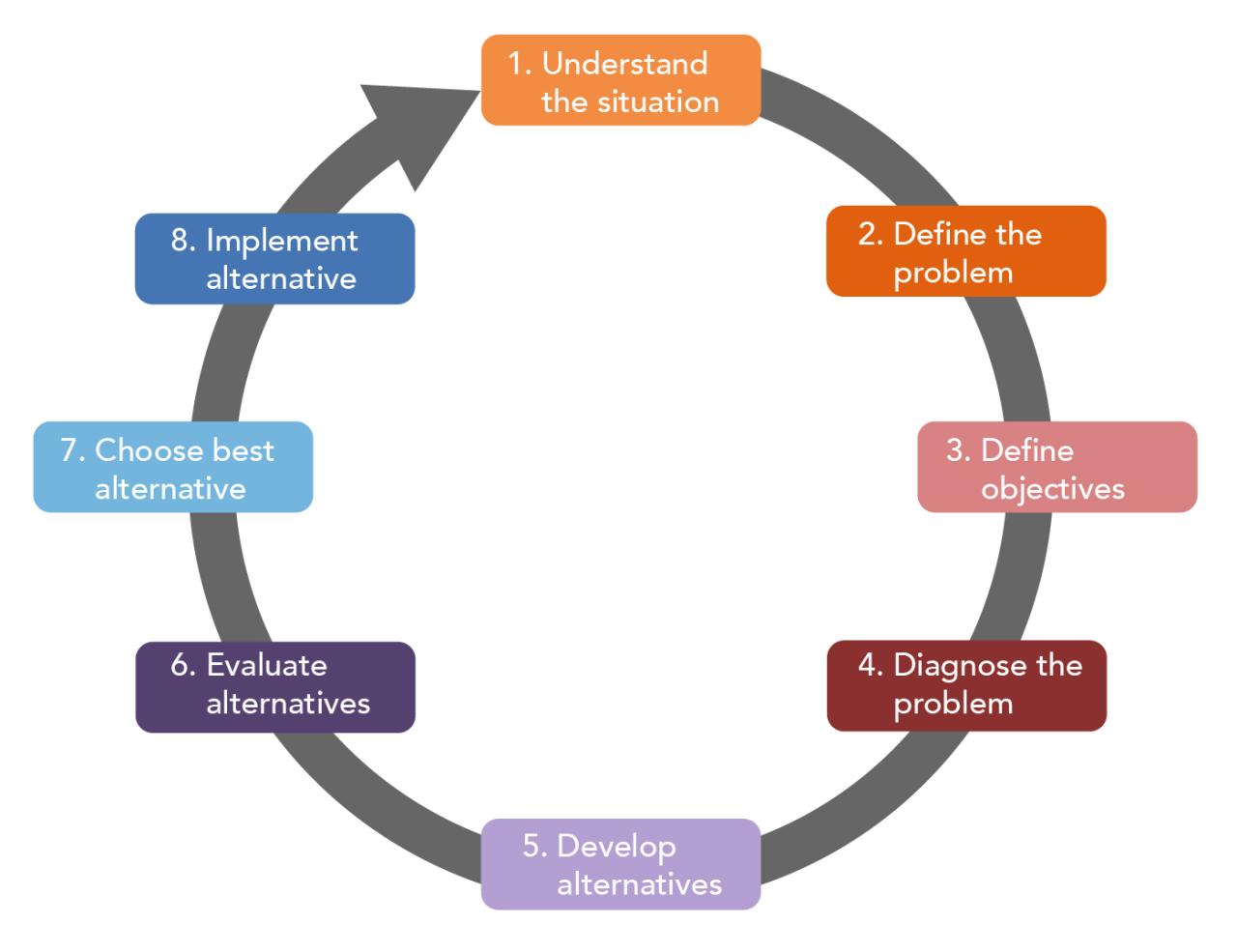
Implementing a rational approach to ship order management, while theoretically sound, faces numerous practical hurdles. These challenges stem from the inherent complexities of the shipping industry, including fluctuating market demands, unpredictable geopolitical events, and the sheer volume of data involved. Overcoming these obstacles requires a proactive and adaptable strategy, one that acknowledges the limitations while maximizing the benefits of a rational framework.The successful implementation of rational decision-making in ship orders hinges on addressing the potential roadblocks head-on.
A well-defined strategy for overcoming these obstacles is crucial for achieving the desired outcomes. A comprehensive understanding of the challenges, coupled with practical solutions, is paramount to achieving a smooth transition and optimizing ship order processes.
Identifying Potential Challenges
Understanding the obstacles to a smooth transition is essential to developing effective countermeasures. Key challenges include resistance to change from within the organization, inadequate data quality and accessibility, and a lack of skilled personnel equipped to handle the complexity of rational decision-making. Cultural resistance to new approaches, often entrenched in established routines, can create significant roadblocks. The complexity of data gathering and processing can also hinder progress.
A lack of readily accessible, accurate, and reliable data can render rational analysis ineffectual. Finally, a shortage of personnel with the necessary analytical skills can limit the successful implementation of rational methods.
Obstacles to a Smooth Transition
Several factors can impede the transition to a more rational ship order process. These include a lack of buy-in from key stakeholders, inadequate training for personnel, and the difficulty in adapting existing systems to accommodate new methods. Resistance to change can stem from a fear of the unknown, concerns about job security, or a perceived loss of control.
Furthermore, insufficient training can lead to errors and inefficiencies, thereby undermining the effectiveness of the new approach. Integrating rational methods into existing systems can also prove challenging, demanding substantial adjustments and potentially significant upfront investments.
Solutions to Overcome Challenges
Addressing the identified challenges requires a multifaceted approach. Strategies for fostering a culture of change, investing in robust data management systems, and developing a skilled workforce are crucial. Promoting open communication, involving stakeholders in the decision-making process, and offering comprehensive training can help address resistance to change. Improving data quality and accessibility, through better data collection protocols and the use of advanced analytics tools, can facilitate rational decision-making.
Investing in training programs focused on data analysis and rational decision-making will develop the necessary expertise within the organization.
Arison’s ship order decisions need to be carefully considered, and a rational approach is essential. Recent events, like Aker halting delivery of building materials for an NCL ship ( aker halts delivery of building materials for ncl ship ), highlight the potential for unforeseen issues impacting the entire process. Ultimately, a methodical and well-thought-out strategy is critical for successful ship ordering, and this is a key lesson for Arison.
Examples of Successful Implementations
Several organizations have successfully navigated similar challenges. For instance, [Company A], a major shipping company, successfully implemented a data-driven approach to ship order management, resulting in significant cost savings and improved efficiency. Their approach involved robust data collection, analysis, and predictive modeling, leading to optimized decision-making.
Adapting to Changing Market Conditions
The shipping industry is dynamic, with market conditions constantly evolving. A rational approach to ship order management must be adaptable to these changes. Flexibility is key to ensuring continued success in a volatile market. This involves regularly reassessing assumptions, incorporating real-time data, and adjusting strategies as market conditions dictate.
Strategies to Adapt to Changing Market Conditions
A rational approach to ship orders requires a dynamic and adaptable framework. Regular reviews of market trends, the use of predictive analytics, and the ability to adjust the order process in real-time are crucial. Regularly reassessing initial assumptions, incorporating real-time data, and updating strategies based on current market conditions are vital.
Table of Potential Challenges, Impact, and Solutions
Challenge | Impact | Solution |
---|---|---|
Resistance to change | Slow adoption, decreased efficiency, potential project failure | Open communication, stakeholder involvement, comprehensive training, incentives for adoption |
Data quality and accessibility | Inaccurate decisions, inefficiencies, missed opportunities | Improved data collection protocols, robust data management systems, advanced analytics tools |
Lack of skilled personnel | Errors, delays, reduced effectiveness | Targeted training programs, recruitment of skilled personnel, partnerships with data analytics firms |
System integration challenges | Disruptions, inconsistencies, increased costs | Careful planning, phased implementation, robust system architecture |
Illustrative Scenarios
Putting rational decision-making into practice in ship ordering requires understanding how different factors influence choices. This section explores scenarios that highlight the importance of a structured approach, demonstrating how a rational framework can lead to optimal outcomes.
Prioritizing a Ship Order
Analyzing the factors affecting ship order prioritization is crucial. A rational decision-making process necessitates a systematic evaluation of competing needs and potential outcomes. This includes assessing market demand, financial constraints, and the technical feasibility of the project. A strategic evaluation is necessary to ensure the ship order aligns with the company’s overall business objectives.
Scenario 1: Choosing Between Two Vessel Types
Imagine a shipping company needs to order a new vessel. Two options are available: a bulk carrier for transporting raw materials and a container ship for cargo transportation. Factors influencing the decision include projected demand for each type of cargo, current market rates, the company’s existing fleet, and the financial implications of each order. A rational approach would involve quantifying the potential revenue streams for each option, comparing the operational costs, and evaluating the risk associated with each vessel type.
A thorough analysis considering all relevant factors will result in a more informed choice.
Scenario 2: Implementing the Rational Approach
This scenario focuses on the practical application of a rational approach. Let’s say a shipping company needs to expand its fleet quickly to meet a surge in demand. Instead of rushing into an order, they conduct a comprehensive market analysis, assessing current shipping rates, anticipated demand, and the availability of qualified shipyard capacity. They develop a cost-benefit analysis to compare various vessel types and sizes, taking into account the required investment and potential returns.
The analysis also factors in potential risks like market fluctuations and delays in construction. This systematic approach to decision-making minimizes the risks associated with the ship order and maximizes the chances of success.
Analyzing Different Approaches
A critical aspect of rational decision-making is comparing different approaches. This involves examining the potential benefits and drawbacks of each option. For instance, a purely cost-driven approach might overlook potential long-term advantages of a more sophisticated vessel, while a purely market-driven approach might neglect the company’s financial constraints. The rational approach requires a balanced consideration of all factors, optimizing the decision for long-term success.
Comparative Analysis Table
Scenario | Factor | Decision | Outcome |
---|---|---|---|
Scenario 1: Vessel Choice | Projected demand for bulk cargo | Order bulk carrier | Successfully met increased demand for raw materials, maximizing revenue. |
Scenario 1: Vessel Choice | Projected demand for container cargo | Order container ship | Efficiently handled containerized cargo, ensuring high utilization rate of the vessel. |
Scenario 2: Fleet Expansion | Market analysis | Order a combination of vessels | Successfully met the surge in demand with an optimized fleet mix, preventing over-investment in one type of cargo. |
Scenario 2: Fleet Expansion | Financial analysis | Negotiate favorable shipyard contracts | Reduced overall investment costs while maintaining the quality of the vessels. |
Last Recap
In conclusion, implementing a rational approach to ship order management is not just about efficiency, it’s about resilience and adaptability. By understanding the principles of rational decision-making, optimizing processes, and effectively mitigating risks, companies can navigate the complexities of the shipping industry with greater confidence. The successful implementation of these strategies, as demonstrated in the case studies, ultimately leads to increased profitability and a more streamlined operation.
This guide aims to equip you with the knowledge and tools to achieve these results.
Clarifying Questions
What are the key criteria for evaluating ship order efficiency?
Key criteria include cost-effectiveness, delivery time, cargo handling procedures, safety protocols, and the overall impact on the supply chain.
How can data analytics be used to optimize ship order processes?
Data analytics can identify trends, predict potential delays, and allocate resources more effectively. It allows for proactive adjustments to changing conditions.
What are some common challenges in implementing a rational approach to ship orders?
Common challenges include resistance to change from stakeholders, inadequate resources (personnel or software), and adapting to unpredictable market fluctuations.
What resources are necessary for implementing a rational approach to ship order management?
Essential resources include trained personnel, appropriate software solutions, accurate data on cargo, vessels, and market conditions, and a clear communication strategy.